Since the age of five, growing up in New Jersey with a father who was an aerospace engineer, fighter pilot, and airline pilot—alum Tom Price dreamed of being an engineer and working in aerospace. He came to the University of Utah because his mom and stepdad both teach here (physics and math education). Tom said, “My favorite part about being a mechanical engineering student were my friends in class. We have gone our separate ways, but some of us are still great friends and we definitely helped each other get through class. Find your friends and buckle in!”
After earning his BS, Tom realized his dream working in aerospace defense at L-3 Communications. He worked in test engineering and then managed one of the largest environmental test labs west of the Mississippi, right here next to the Salt Lake City airport. There he spent his days trying to break everything from radio equipment to large drones. The objective was to make sure that before leaving the facility, the designs and products could reliably survive the rigors of their intended environment.
“Simulating heck on earth isn’t easy. To do so required fun tools like liquid nitrogen, cooled thermal chambers big enough to park a car, which could plunge and bake equipment, altitude chambers big enough to walk into, and giant electrodynamic speakers (shakers) large enough to bolt parts onto with amplifiers measured in the hundreds of kilowatts.”
However, learning the ways of Fortune 500 engineering companies and the glacial speed they move, wasn’t exactly what Tom anticipated. From L3, he went to Silicon Valley to lead the hardware test engineering team and run the engineering lab at a hospital equipment company, Omnicell. At the time Omnicell was embarking on the biggest new product the company had ever made.
For this new product, Tom saw a need for large scale 3D printing, but his workplace didn’t agree. Tom responded by buying one for himself. “I bought the 3D printer as a continuation of my hobby. After listing it online, people started asking for quotes. Like myself, others found there are not a lot of options for really large engineering grade rapid prototyping. Plus they are extremely expensive. I discovered that maybe there was something to this,” said Tom.
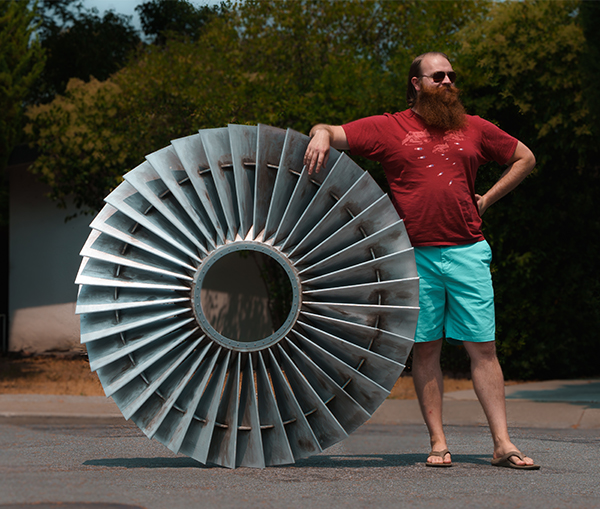
From Omnicell Tom went on to be the director of engineering at an automation company L2F, which did automation projects from Silicon Valley food tech companies. For example, L2F did welding of rocket engines for SpaceX. Meanwhile Tom’s after-hours hobby with large scale 3D printing continued to grow. “I started to need more 3D printing machines to handle demand. Then one week my 3D printers sitting at home started making more than I did sitting at work.” (Pictured top of page is Tom with a 20 foot by 20 foot 3D printed model of Cupertino after the new Apple Headquarters went in.)
“It started happening more frequently and with increasingly complex and challenging projects. One week I was printing enclosures to test fit equipment for a CT scanner, then the next was autonomous car parts. Weird projects that needed really big parts started finding me. One of my favorites was shipping fixtures to China for manufacturing, because I was faster and could do a better job than they could!”
In November 2018 Price took the plunge and quit his day job to focus on 3D printing full time at Titanic Design. “It’s fun and exciting and a whole new set of problems to solve!”
Today Tom spends his time 3D printing huge parts for companies, entrepreneurs, and institutions. When not 3D printing for others he usually ends up 3D printing for himself. Tom also likes to travel, is an amateur photographer, and brews beer. He is currently up to 33 countries, has walked across England coast to coast, and summited Mt. Kilimanjaro. Additionally, he is finishing his road tripping up and down the west coast of the United States.
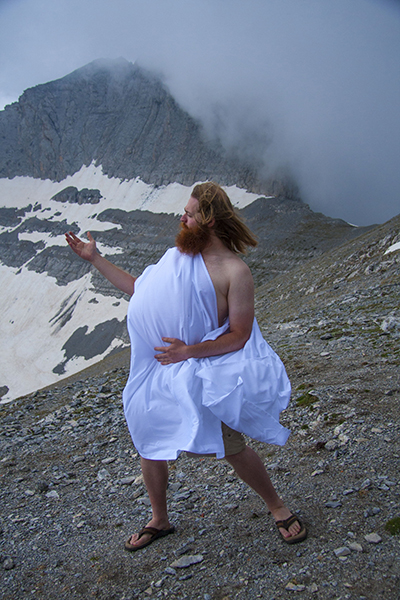
Tom Price’s thoughts on 3D Printing:
- Additive manufacturing has been around for decades and now completely dominates the first prototyping stages of the design cycle. It is also finding a place in the list of standard manufacturing technologies with the value it brings.
- Small format 3D printing now is effectively a commodity with hundreds of 3D printers and huge ranges of options. It will never replace other traditional forms of manufacturing but is another tool to complement them. Entire cars and jet engines have been made with 3D printing but they are demonstrators.
- Most production parts will most likely be made fairly similarly to how they are made today. Injection molding is cheap and fast per part, machining is accurate and strong, more than 90 percent of parts will stay the same.
- You probably won’t be living in a 3D printed house (at least not anytime soon). However specific components have been totally replaced by the advantages of 3D printing. The combustion nozzles in jet engines are now being made using direct metal laser sintering. Your new hip will probably be 3D printed so that the bone will properly grow into it.
- There are probably parts hidden unassumingly in your commercial equipment where 3D printed parts let the product be released to market when one of the part numbers had an issue during production and is being used until the tooling gets fixed.
Tips for today’s mechanical engineering students:
Find an internship or otherwise get real world experience. Understanding how engineering works in the professional environment and business is critical. The best engineers understand how to navigate a workplace and can articulate and communicate their ideas and concerns. The more places that you work the broader your experience and the more you can identify the common denominators and get things done.
- Look at the bigger picture of what you are trying to solve and deliver a solution that does not just fulfill the task you were given but solves the problem. Try to work yourself out of a job. Nine times out of ten you get rewarded with bigger and more challenging problems to solve.
- Make mistakes and take risks. Work is about learning. A good company and manager provide employees with a safe place to try new things and improve old ones. You learn to be a better engineer and they get a better product. When you stop learning, start looking.
- Look for the extra opportunities. If you get a chance at work to go on a factory tour of China, take it. It will blow your mind and make you understand how to design and make products better. Assembly is where a huge number of products have issues. Interact with other groups, manufacturing, and your customers. Seeing the bigger picture and solving the real problem lets you keep learning versus your manager giving you a one way ticket to China to fix your parts on the factory floor while everyone is hassling you.
- No one has any idea what they are doing. Find your peace with that and figure things out and have fun doing it!