Industrial turbines that burn natural gas currently generate about 40 percent of the US’s electricity — and nearly 15 percent of its carbon emissions.
Natural gas isn’t the only option for turbines, however. Pure hydrogen is a highly flammable fuel option that produces mainly water vapor when burned, qualities that would seem to make it an ideal green power source for these sorts of plants.
The problem is that hydrogen is too flammable to be readily used as fuel. Gas turbines are specifically designed for the combustion properties of natural gas. Hydrogen is a much more reactive fuel, and is much smaller on a molecular level, making its flames much harder to control without damaging the turbine itself.
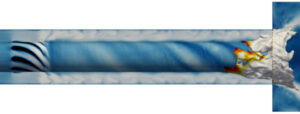
“One of the main obstacles slowing the transition to hydrogen use in gas turbines is flame flashback, a phenomenon wherein the flame proceeds upstream of the thermally protected combustor with catastrophic consequences,” says Price Engineering’s Alex Novoselov.
Novoselov, assistant professor in the Department of Mechanical Engineering, has received a National Science Foundation CAREER Award to study this phenomenon. He’s using advanced computational simulations in a search for the fundamental physics that govern flashback, as well as for ways to design around it.
Many natural gas plants already have the capability to mix hydrogen into the flow of burning hydrocarbon gases, cutting the net carbon emissions per watt generated to a small degree.
However, cutting additional carbon emissions requires blending even more hydrogen which is a challenge for most existing systems.
“While gas turbine manufacturers anticipate 100 percent hydrogen utilization in the future, current industrial turbines have the potential to operate closer to 50 percent hydrogen by volume,” Novoselov says. “Beyond that, the risk of boundary layer flashback is too high for the turbine to operate safely.”
Managing a turbine’s flame means carefully balancing the flow of fuel and air into the combustor with the speed at which the flame propagates. One complicating factor is that the flow moves more slowly along the walls of the combustor than in the middle; a too-fast flame can burn through this slower boundary layer, potentially escaping the combustor entirely.
“Because hydrogen is more reactive and mixes faster, the more hydrogen we add into the fuel, the faster the flame speed,” says Novoselov. “At some point, the flame speed becomes faster than the flow, especially along the boundary layer, increasing the likelihood of flashback. And only the turbine’s combustor is designed to handle the intense temperatures involved, so this has the potential to damage or destroy the rest of the equipment. ”
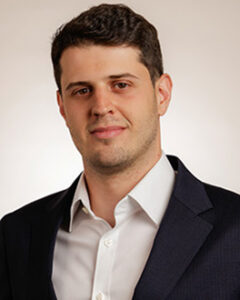
Novoselov’s CAREER Award will support foundational research into boundary layer flashback, and critically, how it can be avoided.
“We’re interested in determining what triggers this instability,” says Novoselov. “Can we understand the physics that turns a stable flame into something potentially dangerous? If so, we can then build models that will tell us how much hydrogen is safe to add to a given system.”
Beyond the ability to better predict the safety tolerances of existing equipment, Novoselov’s simulations could eventually aid in designing next-generation turbines, purpose-built to run on much higher concentrations of hydrogen.
Some of these projects have already begun to take shape. For example, the Intermountain Power Agency’s IPP Renewed Project, based in Delta, Utah, aims to run off of pure hydrogen by 2045.
“IPP is currently aiming to run at 30 percent hydrogen this year, giving them 20 years to make up that difference,” Novoselov says, “With our fast, reliable models of flashback, we think we can significantly accelerate that progress across the field.”