Design Day - Spring 2019
Design Day is an opportunity to share our Senior Design Showcase with the public. Seniors work in groups with faculty to design and test projects.
Additionally, freshman and junior mechatronics’ students compete and showcase their skills.
Senior Design Projects
The manufacturing process of Varex’s X-Ray Tube Shield Can is currently done manually. Manual assembly takes up a large portion of the technician’s day, for this reason, Varex has sponsored us to automate the process in order to allow the technician to tend to more important matters throughout the day.
Team: Chris Alvarez, Kaden McDonald, Chris Pearson, Isabella Thayne (lead), Spencer Totsch, Shane Williams, Matt Wilson
Advisor: Dr. Shad Roundy
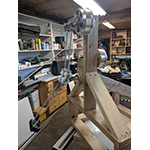
Advisor: Dr. Wenda Tan
The goal of this project was to design and build a vehicle to compete in National Fluid Power Association’s Fluid Power Vehicle Challenge in order to gain knowledge and experience with fluid power components, circuits, and systems. The team gained experience working as an engineering team, developing an idea from concept to demonstration, and had the opportunity to network with mentors in the fluid power industry. (Fluid Power Vehicle Challenge Poster)
Advisor: Dr. Kuan Chen
The objective of this project was to improve the performance of the Formula U racecar by adding a lightweight, composite undertray to the vehicle. The undertray increases downforce and decreases drag, improving the existing aerodynamics package and allowing the vehicle to handle better in corners, thereby decreasing lap times. Computational Fluid Dynamics modeling was used to optimize the geometry of the undertray for maximum performance increase, and carbon fiber composite manufacturing processes were used to create a lightweight, but rigid final product. A quick disconnect latching system was designed and implemented to allow for easy removal of the undertray, which is necessary to access the car’s battery system. The undertray will both increase performance scores at competition, as well as increase the team’s design score, resulting in an overall more successful competition. (FSAE Composite Aero Package Poster)
Advisor: Dr. Sam Drake
Electrospinning consists of drawing polymer from a charged reservoir to a grounded collection area. The resulting nano-scale fibers form fabric -like materials whose high strength and surface-area-to-volume ratio make them desirable in a variety of filtration, textile, and medical applications. The goal of this project is to construct an inexpensive, portable electrospinning device as an alternative to typical expensive and fixed contraptions, for use in educational outreach. (Generating Programmable Nanofibers Poster)
Team: Filzah Athirah, Zuhair Aziz, Dallin Romney (lead)
Advisor: Dr. Jiyoung Chang
Our team had a dream of creating a cloud that would engulf the feet in fog. This, in turn, would allow us to create the illusion of floating like a ghost. Thus Ghost Walks was born from our team coming together and boldly proposing a student project to give life to this dream. As our senior design team has moved forward, we have discovered that making a small prototype, that has the ability to produce fog, would achieve our goal.
Home Biofilter is a project that is intended to tackle the air pollution in the indoor areas using a filtration system that operates using natural processes as its based system, for example, aeration and hydroponic system. The design will be able to filter contaminated air in the house, specifically houses or rooms without proper air filtration system. The system will be autonomous and the design will be running whenever the sensors placed on the design detect readings above the set or recommended air quality levels. There is also an LCD display put on the design to display the readings. Staying indoor should be safe while avoiding bad outdoor air, and indoor air quality should be better than the outdoors even in an area with high air pollution levels. (Home Biofilter Poster)
Advisor: Dr. Steven Naleway, Max Mroz
The purpose of this project is to design an automated test apparatus that applies controlled, cyclical impact loads to samples of Ti-64 that are produced using additive manufacturing methods. The system is designed to accept user inputs that define impact velocity, spring constant, and material properties. These inputs define system parameters that determine the air pressure, compression displacement and period of the test. The system will display, in real time, system pressure, measured velocity, and number of completed cycles. (Impact Fatigue Test Apparatus for Additive Manufacturing Samples Poster)
Team: Arif Afzal, Brandon Corwin (lead), Huren Suthar, Nor Zaki
Advisor: Dr. Owen Kingstedt
Lifting Coach is designed to reduce workplace injuries that occur from repetitive strain, heavy lifting, unsafe practices, and poor lifting form. Injuries that result in worker’s compensation cost billions of dollars per year and measuring exposure to common risk factors such as lifting, lowering, pushing, pulling, and carrying, with high precision is challenging. Lifting Coach seeks to enable continuous data collection of foot pressure, foot position, and foot movement to quantify risk via IMUs, position sensors, and gait analysis. This data can then be used to provide meaningful feedback to the user to reduce or prevent future injuries. (Lifting Coach Smart Insole Poster)
Team: Thackery Archuletta (lead), Craig Butler, Nick Smith, Jaron Stevens, Steven Turner, Mitch Wheat
Advisor: Dr. Andrew Merryweather
Nordic sit skiing is a sport that requires immense upper body strength for people with disabilities. Current sit skis require that the skier must push themselves uphill and slow themselves going downhill. Our team has been tasked to create a power assist device that can help the user go up hills without extreme effort and slow them down while going downhill. The device will be ideally be contained in the area between the two skis and underneath the saddle of the sit ski. (Nordic Power Assist Poster)
Team: Siti Azmi, James Bailey, Christopher Holland, Emily Mitchell, Shiv Patel (lead), Ahmad Zaman
Advisor: Dr. Andrew Merryweather
The most commonly available bionic knee on the market costs about $100,000. Our group’s goal is to find a way to reduce that cost significantly by using open-source techniques that allow for STEM students and “makers” to reproduce our work and see how they can improve it. The goal is to allow people who are interested in learning more to have a much lower buy-in.
Everything we do to produce the knee has to be repeatable with training that undergraduate level STEM students can achieve. All coding, computer-aided drafting and analysis will be open-source for reference and as building blocks for any other interested users. Our initial prototype cost around $450 to produce with the use of a lathe, mill and basic shop tools. (Open Leg Bionics Poster)
Advisor: Dr. Tommaso Lenzi
Utah’s bionic ankle has been developed to more closely mimic the biomechanics of the natural ankle to make locomotion easier for transtibial amputees and to advance mechatronic prosthetics. However, in order for the user to fully benefit from this progressive ankle, a suitable foot must be developed that takes into account Utah’s bionic ankle’s weight and active control capabilities. The goal for this project is to design a passive prosthetic foot, analyze the parameters to achieve an energy efficient foot and manufacture a lightweight, strategically compliant prosthetic foot without using electromechanical properties to work in tandem with the bionic ankle. (Prosthetic Foot for Bionic Ankle)
Advisor: Dr. Tommaso Lenzi
One of the most important roles of an engineer is to save lives through innovation. With around 42% of construction fatalities occurring from falls, there is a clear need for improvement upon the current fall arrest protection systems. On top of this, OSHA has very strict regulations on what is and isn’t allowed with these systems. While some systems are convenient and quick to install, they fall short in reliability during an incident. Some systems check all the requirements prescribed by OSHA, but are inconvenient and expensive, making them nonviable for small-scale crews. This project will strive to find balance between following the requirements of OSHA and creating a system that is both safe and viable for teams of all sizes.
Team: Hunter Bernstein (lead), Clancy Van Dyke, Gary Hsu, Aimee Morgan, Kyle Somer, Zachary Zwahlen
Advisor: Dr. Kenneth d’Entremont
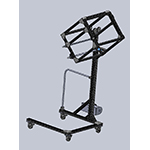
Advisor: Dr. Jacob Hochhalter
Commercial hammocks such as ENO and Kammock have become increasingly popular for backpackers and hikers. An issue with the system is that there needs to be two trees at the right distance to set up these hammocks. Our project tackles this issue by allowing these hammocks to be hung from just a single tree. Our single anchor hammock support system is comprised of two components consisting of lightweight aluminum and axially braided carbon fiber. These components give the user the option to setup their hammock from a branch or from the trunk of a tree. Altogether the system weighs eight pounds and can be broken down into pieces that fit in a single person tent bag. By fitting into a hiking backpack and weighing slightly more than a tent, this system is an alternative to traditional tent camping. (Single Anchor Hammock Support Poster)
Team: Ahmed Allogani, Starley Bush, Tysen Heaton, Joshua Mathieu, Andrew Spink (lead)
Advisor: Dr. Ken Monson
The purpose of this project is to create a novel solar-powered ice-maker attached to a traditional ice-cooler over the course of multiple senior design projects. This attachment will allow for extended use without needing to store extra ice, as is the current norm. Our team, as the second iteration, is making improvements to the original team’s prototype making it more efficient, environmentally-friendly, and reliable. The upgraded prototype is designed to be durable enough for use in remote environments, such as those found along navigable rivers. It provides a long-term refrigeration solution to these remote areas with minimal user attention and maintenance. Our new design implements a more efficient compressor, a forced-convection heat exchanger, an environmentally-friendly refrigerant, and a re-designed circuit. (Solar Powered Ice Maker Poster)
Team: Alex Beaufort, Carl Fauver (lead), Miguel Granda, Joseph Phillips, Riley Swann
Advisor: Dr. Kent Udell
Actuators can be made by wrapping polymer line with copper then coiling the wrapped polymer. The supercoiled polymer can contract up to 20% with thermal heating and act as an artificial muscle. The objective of this project was to design a mechatronic system that can rapidly contract and extend the actuators so the mechanical force can be transmitted from the muscle. The objective was achieved by running an electrical current through the muscle while embedding the muscle in a tube with flowing cooling fluid, allowing us to control the temperature and consequently the amount of contraction. The success of this results in the output of mechanical force moving a robotic hand. (Robot Muscles – Super-coiled Polymer Actuators Poster)
Team: David Castanedo, McKay Chamberlain, Taylor Liljenquist (lead), Charles Nelson, Ruben Soriano, Yisarai Valbuena
Advisor: Dr. Stephen Mascaro
Medical researchers have requested a device to increase the time efficiency of transferring zebrafish from a petri dish to individual wells. Currently researchers use 5mL disposable pipettes to individually “hunt” down zebrafish and transfer each one to their assigned well; which is time and labor intensive. The goal for this project is to design a fully automated device that is able to dispense zebrafish individually from a large group of fish. The dispensing device dispenses embryos using a syringe pump and a photo sensor to sense fish passing through the dispensing channel. (“The Zipper” Zebrafish Dispenser Poster)
Team: Dan Lee, Hanna Nizam, Brett Reeder (lead)
Advisor: Dr. Bruce Gale
There is a need to validate building energy modeling microclimate software (EnergyPlus, Quic, etc.) used by researchers and engineers in the HVAC industry. The goal of this project is to design and build a small-scale, portable, and durable testing facility, bypassing actual full-scale building construction. The tiny testing facility (TTF) records data to be compared with the heating/cooling load calculations output using the respective software. (Tiny Test Facility Poster)
Team: Matt Ludlow, Moriah Henning, Alex Piccolotti, Issac Rydalch
Advisors: Dr. Amanda Smith, Jermy Thomas
Freshman and Junior Competitions
Building a Better Mars
ME EN 3230 Mechatronics COMPETITION
Utah engineers have been visiting Mars for years to prepare the surface for sustaining life. This year, robots will build further infrastructure to accommodate the influx of Mars settlers. Due to an error in the landing sequence, the lander has damaged its cargo bay and reactor during a crash landing on Minor’s peak. After landing on mars, robots must exit the lander and build crucial settlement buildings before the communication window runs out. Robots must also quarantine the irradiated reactor materials for further decontamination. Before the communication window is over the robots must return to the lander to recharge. Alliances will compete against one another to finish the course with more points by building, sorting materials, and performing operations.
Angry Birds
ME EN 1010 freshman COMPETITION
Sixty nine teams of angry birds have gathered to demonstrate their programming skills and save their eggs from the pigs. The birds have upped their game and are using robots instead of slingshots to launch themselves at the pigs. Each team of angry birds will control an identical robot, which must be programmed to hit six randomly located pigs. Teams must first use MATLAB programming to correctly identify the coordinates of the pigs in a provided satellite image and transmit them to the microcontrollers on-board their robots. Their robots must be programmed to autonomously aim, shoot, and reload. Points will be awarded for locating and hitting each pig, with time acting as a tie-breaker.
“GLOBAL SOLUTIONS” Water Pump Design:
ME EN 1000 DESIGN COMPETITION
According to the World Health Organization, 1 in 10 people worldwide lack access to safe water. Providing improved drinking water sources for at-risk populations has been named by the United Nations as one of the top priorities of the new millennium. The preferred solution, especially in rural areas, has been to establish infrastructure for pumping water from protected wells. This has allowed people to abandon the practice of using polluted surface water, such as from lakes, rivers, ponds, and open irrigation canals, for drinking, thereby greatly improving health in the local area.
Students in ME EN 1000 were tasked with the design challenge of creating an inexpensive water pump as an “off-the-grid” solution to this problem. In the real-world application, water pumps are expected to use human-power from a bicycle. During the design competition, however, to ensure consistency and fairness, a small DC motor is used to power the pumps. Each team is provided with a MakeBlock starter kit and a budget for parts from a local hardware store. Teams design and build their systems using SolidWorks and hand tools, along with 3-D printers to fabricate custom parts. Teams are required to integrate practical course concepts into their designs. Teams are scored based on the mechanical efficiency of their pump and output produced, measured in terms of the volume of water pumped in two minutes. Winning teams will most definitely be the ones demonstrating the strong engineering skills.